Innovating Lab Equipment Accessibility through 3D Printing
Written on
Chapter 1: The Role of Microfluidic Devices in Science Labs
Microfluidic devices play a vital role in numerous scientific laboratories. These devices include mixers, cell culture chambers, droplet generators, multi-layer gradient generators, flow resistors, integrated electrodes, and porous membranes, among others. Researchers at the Singapore University of Technology and Design (SUTD) are developing a 3D printing framework aimed at increasing the accessibility of these crucial tools.
The current methods for fabricating microfluidic devices are both slow and costly.
Section 1.1: Traditional Fabrication Techniques
The predominant method for creating microfluidic devices is soft lithography, where elastomeric materials are molded in a cleanroom environment. Despite its effectiveness for crafting microfluidic channels, soft lithography is a manual and labor-intensive process that poses challenges for automation. Typically, the design-to-prototype cycle can take several days, which is not ideal for rapid development.
Section 1.2: The Promise of 3D Printing
3D printing is emerging as a promising alternative to traditional soft lithography. This technology can transform designs into functional prototypes within hours, and the advent of budget-friendly 3D printers has made this technique more accessible to a broader range of researchers. However, certain limitations still exist, including:
- The range of materials available for 3D printing (e.g., optical clarity, flexibility, biocompatibility).
- The precision of microchannel dimensions achievable with commercial 3D printers.
- The challenge of integrating 3D printed microfluidics with functional materials or substrates.
Subsection 1.2.1: Addressing 3D Printing Challenges
The SUTD team utilized a Direct Ink Writing (DIW) 3D printer to apply a rapidly curing flexible silicone resin onto various substrates, forming microchannels. By interfacing this silicone with another flat substrate, they created microchannels with adjustable dimensions. This innovative method enabled the fabrication of channels as narrow as 32 µm and as tall as 30 µm. They developed basic microfluidic designs (e.g., straight and branched channels, mixers, chambers, and droplet generators) alongside functional designs (e.g., valves, variable flow resistors, and gradient generators) on an optically clear substrate. This technique can also be adapted to create microchannels on a wide variety of functional substrates.
Section 1.3: Practical Applications and Future Implications
The researchers showcased their method by producing microchannels on an unaltered printed-circuit board (PCB), enabling the interface between fluids and electronic circuits. They also created microporous membranes for culturing human keratinocyte cells, a crucial component for wound healing. This approach allows for rapid prototyping of microfluidic devices that integrate essential components for "lab-on-a-chip" applications, enhancing current 3D printed microfluidics that are limited by accessible dimensions and material options. This technology holds significant potential for use in developing countries, where laboratories often face shortages of essential resources.
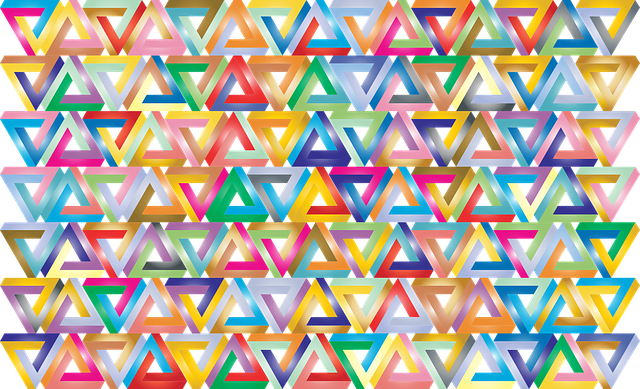